Hazard Identification, Assessment, and Control
Hazard assessments are crucial for protecting people, property, and the environment because they serve as a proactive and systematic approach to identifying, assessing, and controlling potential risks in various environments.
Hazard Assesssment Standard
The Hazard Assessment Standard outlines UCalgary’s framework for hazard identification, risk assessment and risk management. The Standard applies to all UCalgary employees, processes, and activities conducted on UCalgary worksites or on behalf of UCalgary and is used to identify and assess the risk to employees, operations, the environment, or stakeholders.
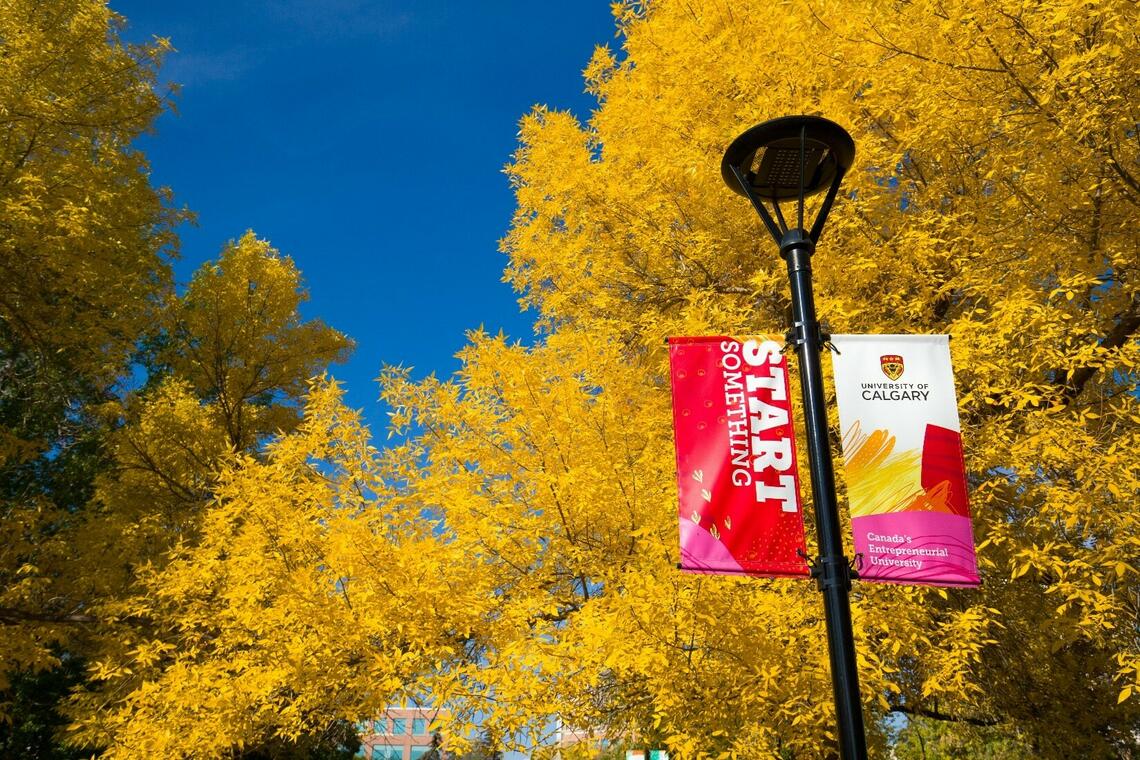
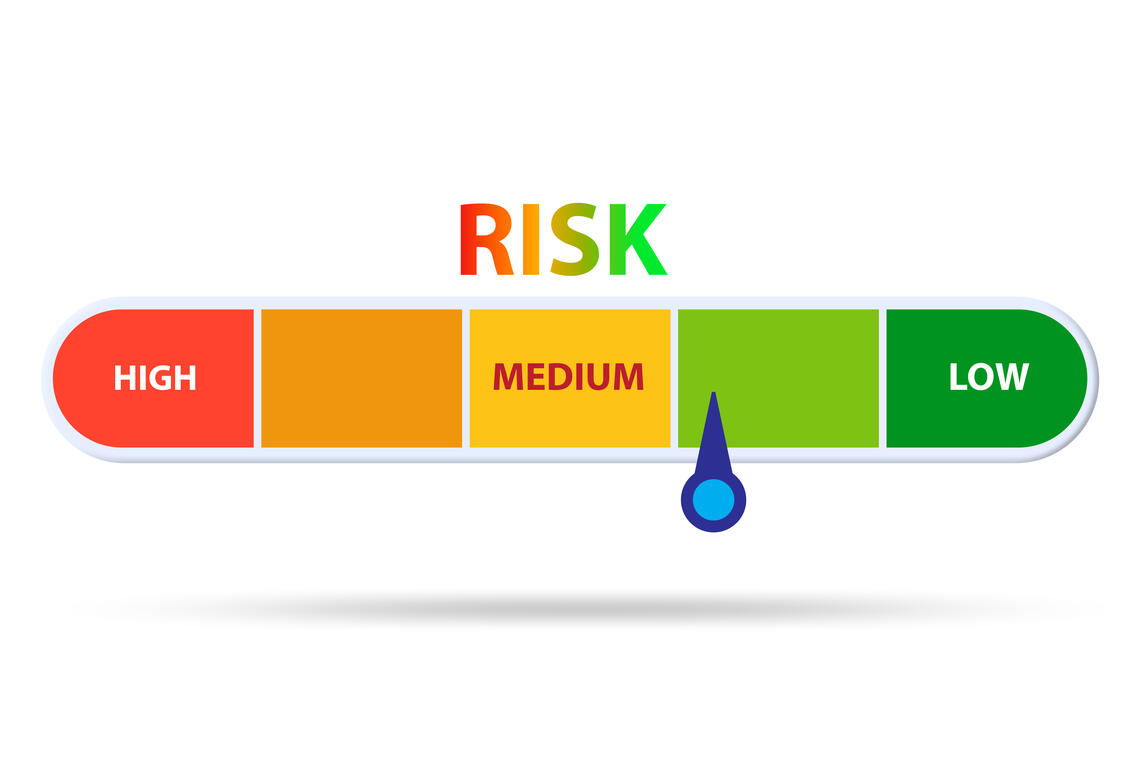
Types of Hazard Assessments
UCalgary has several types of hazard assessment forms and templates to address the wide variety of activities occurring across a diverse range of disciplines, fields, and environments. Hazard assessment types addressed in the Standard and the Procedures include the Hazard Assessment and Control Form (HACF), Field Level Hazard Assessment (FLHA), and Registers. Other types of hazard assessments can be found within their respective Standard such as Field Safety, Confined and Restricted Space Entry, etc. or as per specific activities.
For the Laboratory Hazard Assessment and Control Procedure and HACF Template, refer to Hazard Assessment and Control on the Lab Safety Program website.
Hazard Assessment and Control Form (HACF) Procedure
The Hazard Assessment and Control Form Procedure provides direction for completion of the HACF Form.
Note
The HACF Procedure corresponds to the HACF Template with an effective date of Jan 1, 2024. Please refer to Section 6 of the HACF Procedure for more details.
HACF Template
HACF are used to evaluate and document activities that are typical and unchanging (e.g. activities related to a business title or workshop space).
Field Level Hazard Assessment (FLHA) Procedure
The Field Level Hazard Assessment Procedure provides direction for completion of the FLHA form.
Note
The FLHA Procedure aligns to the FLHA template with an effective date of Jan 1, 2024. Please refer to Section 6 of the HACF Procedure for more details.
FLHA Form
FLHA are used to assess and record activities that are not typical or where conditions can change frequently (e.g. travel to a conference or day trip within Calgary).
Register
Registers are a topic-specific document that outline known or potential hazards and controls for reference purposes (e.g. hybrid work (working from home) or felling trees). Select information from a Register can be added into a hazard assessment, or the entire Register can be added as an additional document to a hazard assessment.
Harassment and Violence Register
Contact Environment, Health and Safety at ucsafety@ucalgary.ca to review the Environmental Compliance Aspects Register.
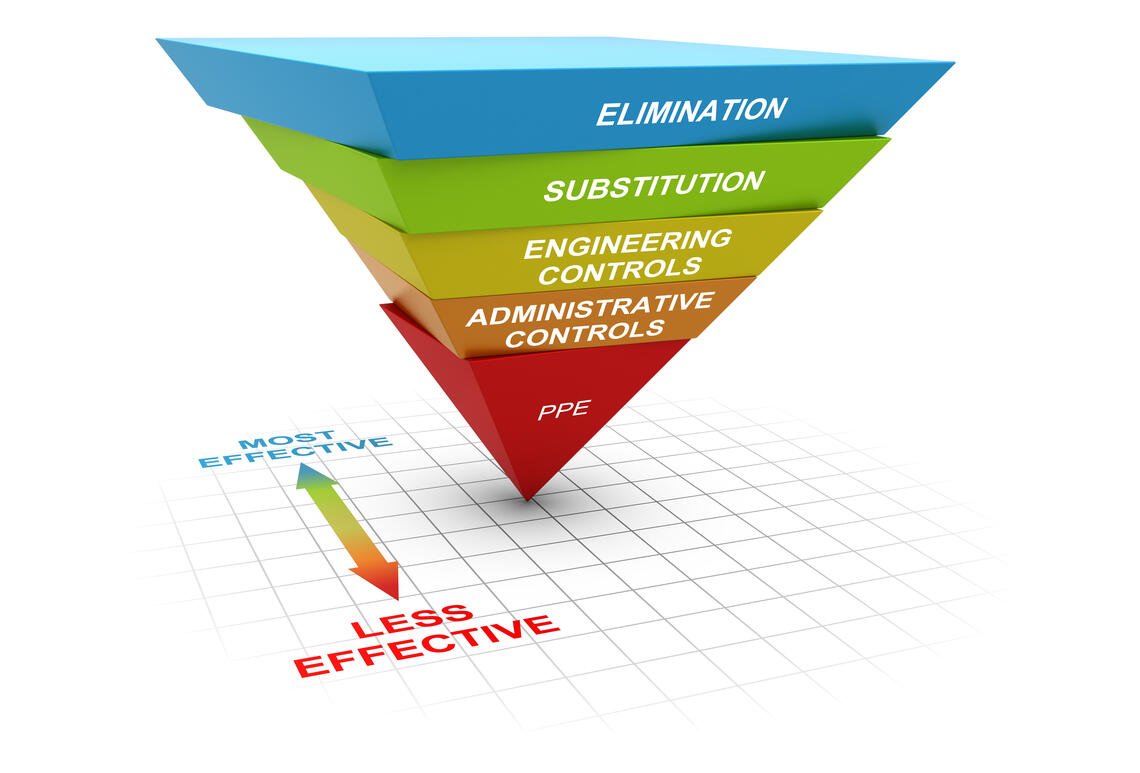
Hazard Assessment eLearning Course
Note – A new eLearning course is in development to align with revised hazard assessment documentation and evolution of the EHSMS. As employees are automatically enrolled into the eLearning course with an established deadline for completion, enrolled employees will need to complete the existing course as instructed. There will be a temporary misalignment between information in the existing course and published documentation; however, we are striving to have this corrected as soon as possible. Contact the EHS Consultant for your Faculty/Department for assistance as needed
Hazard Assessment FAQ
A hazard assessment is a process to document identified hazards, risks, and controls in consideration of activities, tasks, and the environment in which they take place.
Hazard assessments are a requirement of the Alberta Occupational Health and Safety Code, and a component in the Hazard Identification and Risk Assessment element in UCalgary’s Environment, Health and Safety Management System (EHSMS). The main objectives of hazard assessments are to prevent accidents, injuries, illnesses, and contamination.
If a hazard assessment is not covered in the examples below, please reach out to EHS for guidance. EHS is ready to help with selection and completion upon request.
Below is a table summarizing updates to documents and the eLearning course.
Provide feedback or sign up for notifications on updates
Collection of personal information
Your personal information is collected under the authority of section 33(c) of the Freedom of Information and Protection of Privacy Act, and is required for updating your email subscription preferences. If you have any questions about the collection or use of this information, please visit our Access to Information page.